General Manager Damien Sauni needed a partner to build a fully custom Rollforming machine — one that could manage the high output of a diverse product offering, with minimal operator intervention. After a long relationship of 40 years, Hayes International was, in Damien’s eyes, the best partner for the job.
Sheet Metal Folder
Hayes Sheet Metal Folders are an efficient and reliable way to produce folded metal parts. They are a fabricated steel construction with accurately machined working surfaces and a full-length backbone chassis to eliminate flexing. Available in 6-meter, 8-meter, and 10-meter lengths with either 16ga or 14ga capacity.
An optional apron-mounted slitter can be included, allowing the operator to cut products after folding when required. Hayes Folders also feature a full-length back gauge stop with numerical control for position and fold angle. The operator console is mounted to the chassis on a swiveling arm fitted with a touch screen control and fully instrumented with functions for clamp, bend and slit. Onboard software allows for a parts library to save and store programs for future use.
ENQUIRE NOW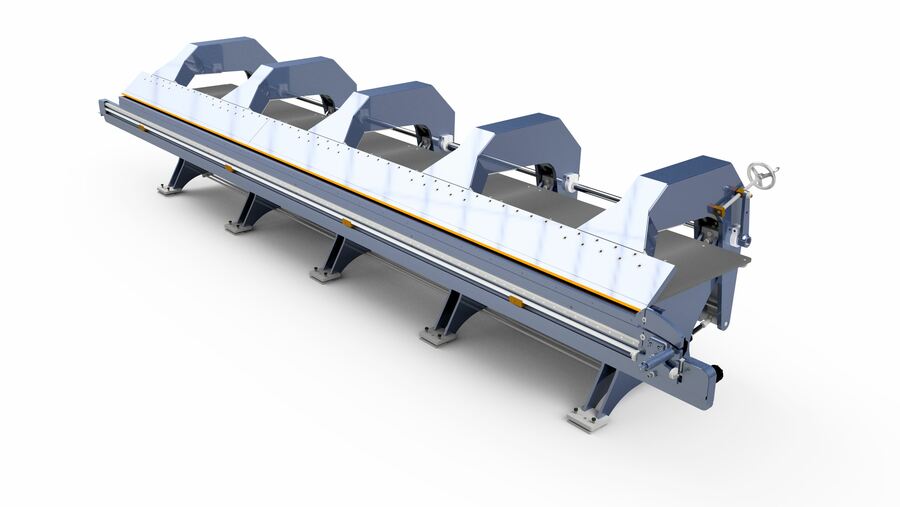
Sheet Metal Folder Standard Components Details
- Welded steel construction with lacquer paint finish.
- Drilled mounting feet with leveling holes for ease of installation.
- Hydraulically powered steel linkages with self-lubricated bushes provide 140° bending capacity.
- Heavy-duty steel clamping jaws with all working surfaces precision machined and polished.
- Removable insert to allow for narrow 'shoulder' type folds.
- Material gauging is set from a single point via a manually set hand wheel mounted on the rear side of the folder.
- Folding action is performed via cushioned hydraulic cylinders for smooth operation.
- Powered via self-contained hydraulic powerpack mounted within folder chassis.
- The back gauge stop is controlled electronically via a toothed belt drive and electric gear motor.
- Incremental shaft encoder with a numerical position for fold angle.
- A foot pedal is mounted below the operator console, and a treadle bar runs the entire folder length, acting as both emergency stops and part of the two-stage clamping procedure.
- The two-stage clamping system raises the folder jaw to a preset height above the folding bed for positioning (mute gap). Operators must depress both safety pedals to complete the clamping process.
- Guarding at all significant pinch points.
- Optional light curtain guards can be fitted for improved safety.
- The operator console is mounted on a swing arm attached to the right-hand side of the chassis.
- Fully instrumented for all main functions.
- Touchscreen controller is mounted on the console used for setting the back stop position and using the included software.
- Hayes software includes a parts library to store and recall parts at a future date.
Request A Quote
If you’re ready to take the next step, let us know below. One of our team can get in touch to talk through your project. If you’d like to share a drawing, attach it below. We look forward to receiving your enquiry.